WSRC-MS-99-00143, Rev. 1
Tritium Effects on Plastics. Studies at the Savannah River Site
Kirk L. Shanahan, Robert J. Reed, Charles J. Coleman
Plastics are used in a variety of places in the tritium processing facilities
at the Westinghouse Savannah River Company in Aiken, SC [1-4]. Thus they
are routinely directly exposed to tritium and suffer from radiation damage.
This effectively limits their process lifetime as typically the properties
that made them useful are adversely impacted. At the point where they must
be replaced, they become radioactive waste. All radioactive waste is categorized
and inventoried at the Savannah River Site (SRS), and a sound technical
basis for this process is desired. Thus the Savannah River Technology Center
(SRTC) has embarked on a program to determine typical tritium content in
waste plastics.
Initial work has focused on the plastic UltraHigh Molecular Weight PolyEthylene
(UHMWPE). One use for this material is in valve tips of earthquake protection
valves. Since these valves are normally open, the tip material sees varying
but continuous tritium exposure over its service life. After considerable
time (1-2 years) the tips blacken and harden and begin to leak, whereupon
they are replaced. Several of these tips have been analyzed recently at
SRS by dissolving and diluting samples of the tip material in water based
solutions followed by subsequent liquid scintillation counting of the
resultant liquid sample.
The exposed plastic tips examined so far have all shown extensive darkening
and even across-the-face cracking. The plastic is embedded in a stainless
steel holder for one type of valve tip, and must be removed to be analyzed.
An Xacto knife is used for this, and it has been observed that the plastic
is quite brittle. It will not so much cut out of the tip as break out
in chunks. In addition a lot of fine and small flakes of material are
produced as well. One type of tip has about 0.5-0.6 g of plastic in it,
while a second type has a larger plastic piece weighing about 1.75 g.
The method places about .09 g. of irradiated plastic in a commercial
Parr Acid Microdigestion Bomb (PADB). The PADB consists of a stainless
steel body fitted with a spring-loaded pressure relief plate. The sample
is placed inside a Teflon liner that slips into the stainless steel body.
A thermocouple is attached to the exterior of the PADB to measure its
temperature.
About 3 ml of concentrated nitric acid is added and the sample is heated
at 150 C for 2 (or more) hours. Less time has resulted in incomplete dissolution,
especially with a sample composed of a few large chunks as opposed to
the more usual powder/small chuck sample. The PADB is then cooled to body
temperature and opened, and the liquid contents are transferred to a 1L
volumetric flask. The Teflon liner is rinsed three times and the rinses
added to the 1L flask. This solution is designated as the `mother liquor'.
At this point the original dissolution solution looks free of solid
material, but does have some NOx gas visibly present. This disappears
as soon as the sample is diluted to volume with deionized water. The Teflon
liner shows an orangish color in the interior. The source has not been
identified, but a nitration product is anticipated. With a 6 hour long
dissolution, the orange color had penetrated to the outer surface of the
liner, which is some 2-3 cm thick. This suggests a possible error if some
T is lost to the Teflon. We have not yet assessed that magnitude of that
error.
Additionally, a small amount of T is lost when the Teflon liner is opened.
The hood air exhaust is monitored for T content, and a small release always
occurs when the liner is opened. Based on air flow rates and air concentration
measurements the loss is on the order of 5-10 Curies T.
Subsequently 0.5 ml samples of the `mother liquor' are diluted to 1L,
and 0.5 ml samples of those solutions are again dilute to 1L, giving a
final dilution factor of four million. This highly diluted sample is then
analyzed by an LSC technique where 1 ml of it is added to 20 ml of Ultima
Gold AB cocktail, and that solution counted on a Beckman LL6000 LSC instrument
for 15 minutes.
All of the sample preparation through the 1L dilutions are performed
in a once-through air flow hood. This hood is continuously monitored for
airborne activity with Kanne detectors. The as received valve tips often
show T release when first received. Working through the plastic extraction
process, this activity tends to decrease with time. Eventually the fractured
plastic tip can be left open in the hood with only slight airborne activity
being noted. Typically, a spike of activity is detected when the PADB
Teflon liner is opened after a dissolution. This quickly drops off as
the sample is transferred to the 1L flask. However, some loss both before
and after dissolution is experienced. Our best estimate of this loss is
that it is on the order of 5 Ci total. (Our current results indicate that
the total T content of the small valve tips is 300-800 Curies.) This may
be in the form of tritiated water, or the dissolution process may produce
molecular HT. Further work is underway to characterize this possibility.
Tritium incorporation into a process material like plastic can occur
by three distinct pathways. The first is by simple dissolution of elemental
tritium into the plastic. However, this tritium is expected to be quite
labile and most likely is not present in the samples by the time they
are dissolved. The second method is by absorbtion of tritiated water into
the plastic. This tritiated water would slowly diffuse through the plastic
and cause slow offgassing as the water reached the surface and evaporated.
Thus depending on sample handling details, some of this material could
show up in analyses. Finally, T can be directly incorporated in the -CH2-
polymeric backbone. The energetic beta decay particles could create free
radicals in the polymeric backbone that would then react with either elemental
T forms or with tritiated water. In addition, when one T atom of a T2
molecule decays, it will leave behind a free T radical, which can directly
incorporate into the plastic. This tritium would not easily leave the
polymer and thus forms the primary source of T that is detected in the
analytical dissolution method. It is unknown if small samples taken from
the tip would show homogenous incorporation or not.
We have repeatedly analyzed select samples to assess the analytical
method's reliability. Sample results are presented as associated with
a valve tip-sample code. This code is a four part one, and is described
as follows. The first part is a simple internal designation (M1) of no
significance at this time since all tips were presumed to come from the
same site. The next part is the tip number (-1, -2, etc.). The next number
is the sample number assigned to one of the .09 g samples. The final code
(D3) indicates the results are from the third dilution, i.e. the sample
that has been diluted 4 million times. Thus samples beginning with the
same two codes (M1-2, M1-3) originate from the same tips.
Within sets of replicates we have observed the majority of results to
be consistent, but individual high values are observed. This kind of behavior
(flyers) could be introduced by either an incomplete dissolution producing
microscopic particulates that appear in random samples, or by some kind
of contamination problem. The samples are prepared with automatic pipettes
using a new disposable tip for each sample. We have attempted analyses
using a sample prepared separately in a cold laboratory from clean UHMWPE,
and have observed no matrix effect. We have observed difficulties with
flyers in similarly prepared tritiated oil standards. We have also compared
a sample dissolved for 6 hours vs. the usual 2 hours and found the same
problem in it.
During studies to isolate the cause of the flyers, we noted that the
samples' T content was increasing with time, as shown in Figure 1. We
traced this to a secondary contamination caused by migration of T, probably
as HTO, into the volumetric flasks by placing another 1L volumetric flash
with pure water in it into the hood. After 24 days the solution produced
259 dpm/ml, and after 34 days it produced 1428 dpm/ml. This has led us
to the realization that we must dissolve, dilute, and analyze the samples
all at once, and that no delays or subsequent resampling of the solutions
are permissible. We will embark on repeat analyses as soon as possible.
Table 1 presents only the first acquired analytical results on several
samples. The data shows some variation within samples taken from the same
tip. It is unknown if this is due to true inhomogeneity in the tips or
not. The Table also shows the estimated T content in Curies per gram sample
and as the weight percent T. Clearly extensive T incorporation has occurred.
Because of the fundamental importance of this type of study, SRTC has
obtained additional DOE funding to conduct full studies of T incorporation
into plastics. We will be exposing plastic samples to T under controlled
conditions to prepare tritium-aged samples. Amount of T incorporation
will be measured, and the effects on physical properties such as brittleness
will be determined.
- M. S. Ortman, L. K. Heung, A. Nobile, and R. L. Rabun III, J. Vac.
Sci. Technol., A8(3) (1990) 2881, and references therein.
- A. Nobile, Jr., Fusion Tech., 20 (1991) 186 and references therein
- A. S. Horen and M. W. Lee, Fusion Tech., 21(2) pt. 2 (1992) 282
- T. Motyka, Fusion Tech., 21(2) pt. 2 (1992) 247
Table 1. Initial LSC Results on T Incorporation in UHMWPE
Sample(*)
|
dpm/ml
|
uCi/ml
|
est. Ci/g
|
est. wt% T
|
M1-2-2-D3
|
1,550
|
0.000698
|
27.9
|
0.3
|
M1-2-3-D3
|
61,700
|
0.0278
|
1110.
|
11.6
|
M1-2-4-D3
|
37,422
|
0.0168
|
674.
|
7.01
|
M1-3-1-D3
|
3,460
|
0.00156
|
62.3
|
0.6
|
M1-3-2-D3
|
38,400
|
0.0173
|
692.
|
7.19
|
M1-4-1-D3
|
66,700
|
0.0300
|
1200.
|
12.5
|
(*) In M1-x- y-D3, x indicates a valve tip, y indicates a sample from
a valve tip
Figure 1. Time Evolution of T Concentration in Volumetric Flasks
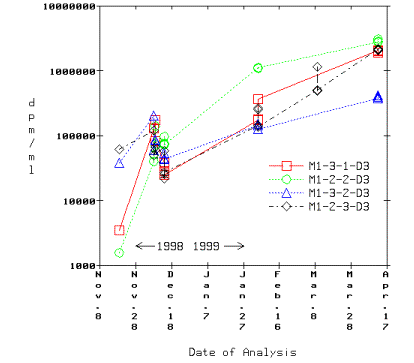
|